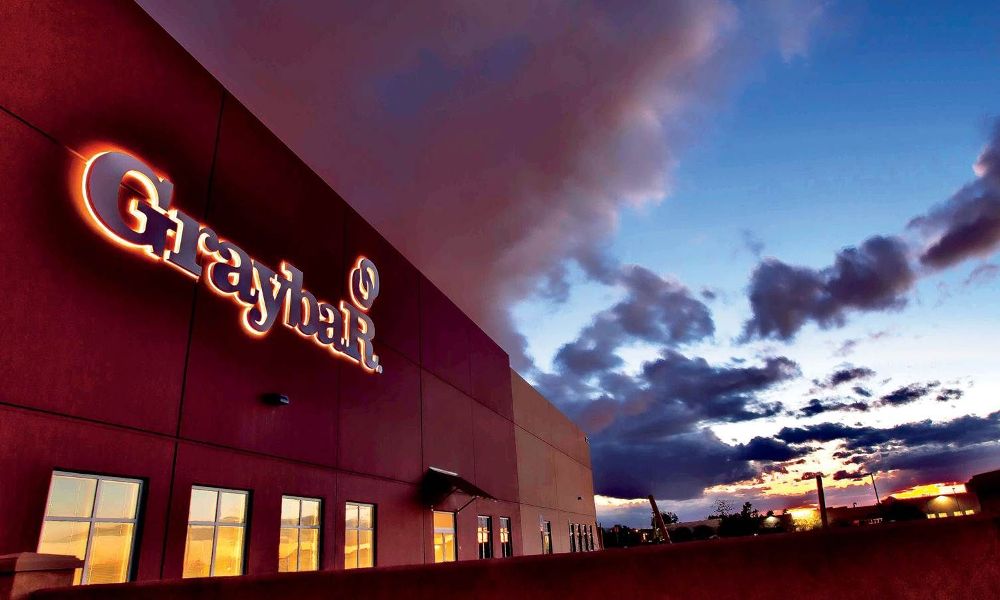
Graybar Electric Company, Inc.
Graybar Rolls Out New ERP, Drives Business Transformation with Data Migration and Master Data Management
Background
Graybar Electric Company, Inc., a Fortune 500 company, is a specialist in supply chain management services and the leading North American distributor of high-quality components, equipment and materials for the electrical and telecommunications industries. Carrying an inventory of more than 150,000 items from over 4,600 manufacturers, Graybar serves as the vital link to hundreds of thousands of customers.
Project Background
To quickly meet customer and supplier demands, Graybar began implementing the entire mySAP™ Business Suite family of business solutions, replacing outdated legacy systems that were incompatible with the future direction of the company.
“For wholesale distributors, effective forecasting, planning and scheduling is fundamental to productivity, and enterprise resource planning is a fundamental way to achieve it,” says Beatty D’Alessandro, Graybar Vice President and CIO. “With the help of SAP Consulting, IBM,® Deloitte Consulting and Syniti, we are rolling out our new enterprise resource planning system. Scheduled for completion in Q3, it will provide a powerful new tool for improving both our supply chain management services and our customer service, while helping us reduce the costs of doing business,” explained D’Alessandro.
Graybar is also deploying a range of enterprise- wide e-business functionality, including mySAP customer relationship management, mySAP supply chain management, and mySAP ERP human capital management.
This project is currently one of the largest ERP (enterprise resource planning) deployments in US history. “Using SAP software as a catalyst, we did a complete ‘replatforming’ and reprocessing of our business to realize our vision of providing cost-effective and efficient ways to deliver our suppliers’ products, services and solutions,” said D’Alessandro. “With the outstanding concepts and methodologies provided by Deloitte and SAP Consulting, we delivered the project on-time and on-budget. Although we still have yet to fully realize the benefits of deploying mySAP Business Suite, as of today, we’ve changed the tempo of the company by implementing electronic handoffs and workflows,” she continued.
The Syniti solution cuts down tremendously on the in-house skills required and on the timetable needed to bring a project from concept to pilot and eventually to production. What can be developed and tested within days using the Syniti solution would take weeks and months using traditional web development tools.”
SAP® Netweaver™ Enhances Functionality
Graybar seeks ways to improve business processes that are or were handled in part by legacy systems. One particular business process is price cost management, which captures supplier requests for changes to their prices, catalog numbers, product descriptions and other information associated with parts. Because of the frequency and volume of these changes (almost 20,000 per day), Graybar needed a cost-effective way to capture the process of approval routing, in addition to the mass updates which require a cascade of interdependent master data changes to the material and product masters. The new solution had to “span and connect” the advanced infrastructure of mySAP ERP with the limited capabilities of the many small suppliers Graybar works with.
“Our objective was to build web-enabled applications that integrated naturally into the SAP NetWeaver platform to capitalize on our existing mySAP ERP and SAP NetWeaver assets. We leverage all that we can within SAP solutions and are committed to use of the SAP enterprise portal component whenever possible. Our philosophy is ‘we don’t code it unless we absolutely have to,’ “explains Joyce.
“We had a tool to handle price cost management, but it was not as elaborate and user-friendly as we would have liked. Because the master data is maintained on our legacy system, we were constantly experiencing problems importing our vendors’ data. We needed to be able to stage and validate this data before it hit the master file – if we had taken raw data and just pushed it through, we couldn’t control the data quality or the timing of when it was applied to the master data. This master data contains everything we need to know about any given part, and many of these factors change over time. For instance, a supplier might notify us that they’re renumbering all their UPCs – our challenge was to load that information into our systems and ensure that it distilled down to all required fields in a variety of business applications,” explains Joyce. “And it needed to be accurate. Imagine the ramifications of having poor-quality data in a database of this complexity and size.”
“The ability to run ‘what if’ scenarios is significant in our business. For example, if a supplier increases their prices by 3%, we need to determine how this will affect our inventory value. And with such large inventory numbers, you can understand the need to uncover any anomalies before we apply calculations of that sort across all our stock,” D’Alessandro said.
“We also have to document and ensure the auditability of all changes. For instance, did we have the authority to change that price? Did it take effect when we said it did? Being accountable in this way is intrinsically tied to the security of our master data and is an element of good business practice that we would adhere to anyway, regardless of the need to comply with regulations such as the Sarbanes-Oxley Act,” Joyce continued.
The ability to run ‘what if’ scenarios is significant in our business. For example, if a supplier increases their prices by 3%, we need to determine how this will af- fect our inventory value. And with such large inventory numbers, you can under- stand the need to uncover any anomalies before we apply calculations of that sort across all our stock.”
Harvesting SAP Platform Functionality
“Our price cost management initiative was one of several targeted for greater automation and
enhanced workflow productivity. We were confident that this functionality could be harvested from the SAP platform – we just didn’t know how to leverage it easily. We chose to develop the Price Cost Management II solution with the Syniti solution because of Syniti’s certified integration with SAP solutions and because it enabled us to rapidly develop web-application functionality using our existing skill sets.
And because we didn’t require highly specialized employees to develop the application, the employees actually using the final solution were the ones involved in development – this meant we didn’t have to worry about any business needs getting lost in translation between business and technical employees. The results have been a remarkable set of composite applications that will serve and enhance Graybar’s use of SAP solutions for years to come,” continued Joyce.
In the new price cost management solution, “intelligent” approval routing allows changes that
fit the Graybar criteria to pass into an automated update while change requests that are unique
or outside contract guidelines are routed to managers for human review and verification. This
routing allows Graybar to decrease the processing time for change requests from the 12,000
suppliers currently using the system, in addition to automating much of the business process. More importantly, the use of a web-application makes it easy for Graybar’s suppliers to integrate their own processes and technologies into the Graybar system
“We built advanced capabilities into the application that help us determine the financial impact of changes. For instance, if a vendor’s change request will impact our inventory levels extremely in one direction or another, the system will highlight this. This provides us the opportunity to explore the issue before the impact is felt by our customers, perhaps by discussing the issue with the vendor before we apply the change,” says D’Alessandro
This master data contains everything we need to know about any given part, and many of these factors change over time...our challenge was to load that information into our systems and ensure that it distilled down to all required fields in a variety of business applications, and it needed to be accurate. Imagine the ramifications of having poor-quality data in a database of this complexity and size.”
Keeping Management Informed
In addition to leveraging the SAP Enterprise Portal as an entry point and framework for many critical business processes, Graybar uses the SAP Business Intelligence (SAP BI) component of SAP NetWeaver to generate reports for management. “We had a business intelligence solution in place on our legacy systems, but as we migrated over to SAP, it made sense to adopt the SAP BI component. This assured us of integration with our other key business functionality now running on SAP solutions and is a much smaller application than the previous business intelligence applications we ran.
Now management receives reports from employees who are trained to produce and analyze reports from SAP BI, and we can pull employee data from our HR system without impacting our transactional system. Because of the large volume of data we store, we want all ad hoc query reporting done at the SAP business information warehouse level – this provides us with improved performance,” says Joyce.
Implementation Highlights & Results
• Syniti enabled web-application development in two-month period without specialized in-house skills
• SAP NetWeaver components reduced costs associated with web-application development and simplified and sped up development process
• Syniti and SAP NetWeaver components enable cost-effective, automated supplier change request process
• Enterprise portal enables simple, centralized access to pertinent information for employees
• Employee self-services save processing costs and time
• The Syniti solution enforces data governance and ensures only clean data enters the ERP system
Future
By year’s end, we expect to have over 80,000 suppliers using the price cost management system. We also expect to work further with Syniti to develop applications that help us maintain mass material, vendor and mass inventory data, and we hope to put those applications online within the next six to nine months. In 2005, we intend to run a campaign to encourage our sales team to use mySAP CRM, and we will likely upgrade to the latest version of SAP business information warehouse,” explained D’Alessandro.
“By implementing the range of SAP solutions, we’ve totally reprocessed and reengineered our HR, finance, and purchasing departments, as well as our order entry, rebate, and pricing mechanisms. While it’s too early to know just how much we’ll benefit, we already have employees in these areas telling us that this is a better, cleaner solution than the previous one. We’re in the process of adapting to significant changes throughout the organization, and we’re all quite certain these changes are for the better,” concluded D’Alessandro.